

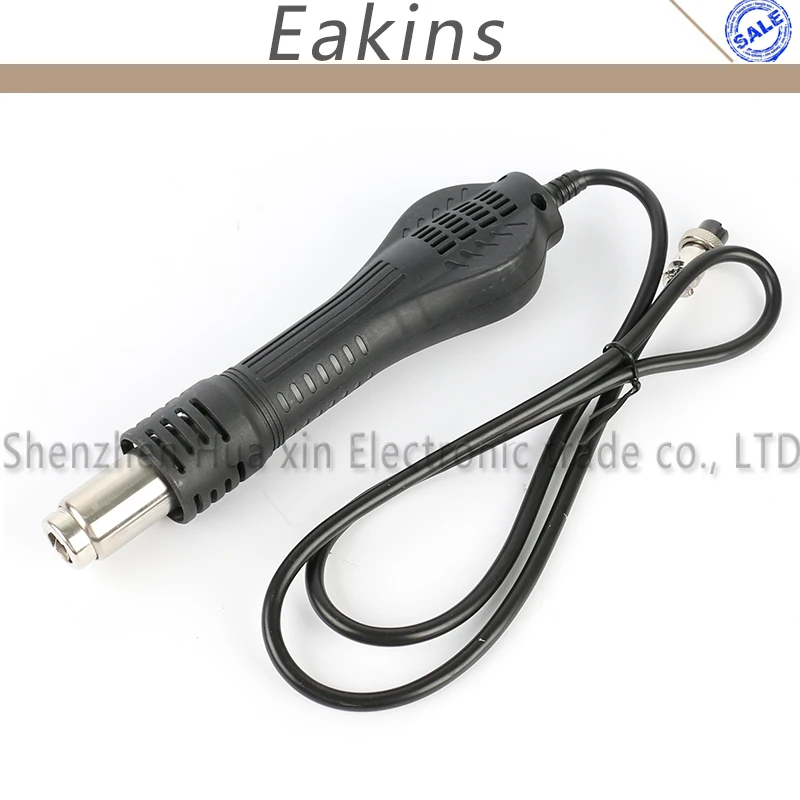
Place a copper braid on top of the first soldered pad and gently press it with the tip of the soldering iron. Turn the soldering iron on and set it at a temperature of 375 degrees Celsius. To desolder an SMD component, first place the board on a flat and dry surface with the component side facing up. Repeat this process for all the remaining component pins. Retract the wire and tip as soon as the solder melts and fills the pad. To solder the next pin, place the solder wire on the interface of the pin and the pad and touch it with the soldering-iron tip. Retract the soldering-iron tip immediately. The solder will melt and the component's terminal will sink to the bottom of the board. Gently press the component from the top with the tip of the tweezers and touch the soldered pad with the tip of the soldering iron. Note that the component will be slightly tilted because one of the pads has solder on it.
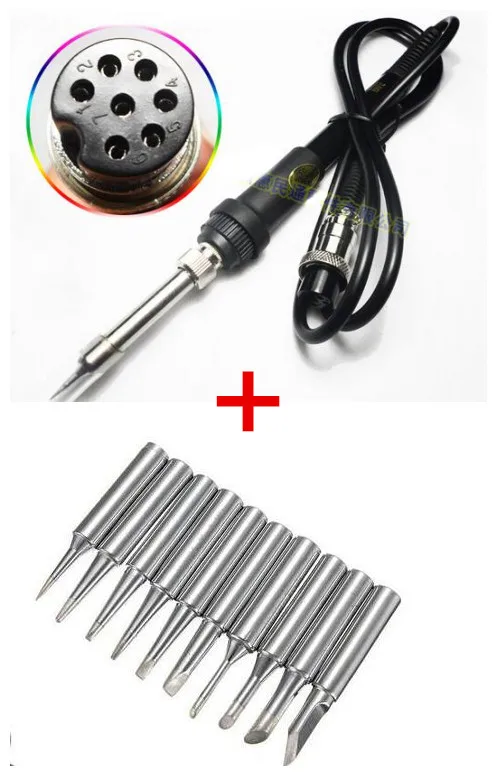
Next, hold the SMD component to be soldered with tweezers and place it on the board so that its terminals get aligned with the corresponding pads on the board. As soon as the solder melts and fills the pad, retract the solder wire and the tip. This can be done by holding the soldering wire on the pad and touching it with the soldering iron tip. Melt a small amount of solder on any one of these pads. Identify the pads on the board where the component is to be soldered. Place the PCB on a flat and dry surface with the component side facing up. Soldering and Desoldering of SMD Components Once finished, turn the board over and pull the component out of the board with tweezers. Repeat this desoldering process for all the component pins. Cut off the front portion of the copper braid that has absorbed the solder flux with a wire cutter. As soon as you notice that all solder flux has been absorbed by the braid, retract the braid and the soldering-iron tip. Within a few seconds, the solder will melt and the molten flux will be absorbed by the copper braid. Place the copper braid on the first soldered pin and gently press it with the tip of the soldering iron. Next, turn on the soldering iron and set it at a temperature of 375 degrees Celsius. To desolder a through-hole component, first place the PCB on a flat and dry surface with the component side facing down. Once finished, cut off the excess component pins with a wire cutter. Repeat this process for all the component pins. Retract the soldering wire and soldering-iron tip. Place the soldering wire at the interface of a component pin and its pad and touch it with the soldering-iron tip. Turn the board over with the component side facing down and place it on a flat and dry surface. Next, turn the soldering iron on and set it to a temperature of about 375 degrees Celsius. To solder such a component, first insert its pins through its corresponding holes on the board and then slightly bend them so that the component does not fall off when board is turned over. Through-hole components are easier to solder because their pads are relatively bigger than the surface mount devices, or SMDs. Soldering and Desoldering of Through-Hole Components The most common method of soldering and desoldering involves heating up the solder flux at a high temperature using a soldering iron. The process of bonding is called soldering, while desoldering is done to remove a component from a PCB. A printed circuit board, or PCB, is populated with electronic components that are bonded with the copper pads on the board.
